Rubber molding

Automotive parts
Gaskets
Construction
Appliances
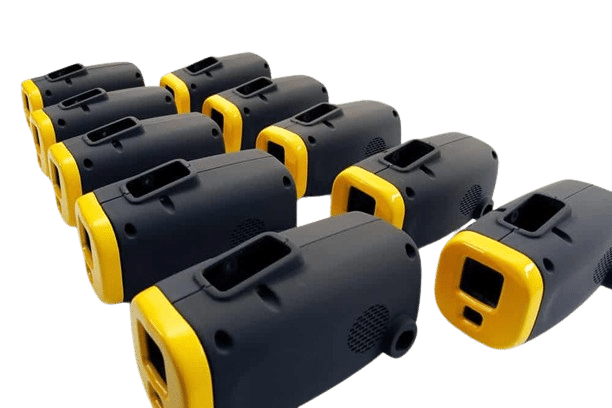
Advantages of Rubber molding
Rubber has good tear resistance and sealing properties. Its one of the most widely used material to make washers, gaskets for enclosures and flexible parts
- Tear resistance
- High flexibility
- Fast molding
- Variable shore hardness
Rubber molding grades
We help you make Rubber molded parts with the properties you need
Standard Rubber types
- Neoprene
- EPDM
- NitrileĀ
Rubber shore hardness
- 20
- 40
- 60
- 80
Design guidelines for Rubber molding
Minimum wall thickness for Rubber parts
A minimum wall thickness of 0.5mm to a maximum of 6mm can be achieved for Rubber parts. Rubber flows well even in small areas
Uniform wall thickness
A uniform wall thickness should be maintained throughout the part to ensure smooth flow of material. Inconsistent wall thickness will hamper filling
Draft angles
ABS injection molded parts generally have a 1 – 2 degree draft to ensure easy removal of part from the mold
Sharp corners
A fillet has to be added in all sharp corners to ensure easy flow of material
Comparison of Injection molded plastics
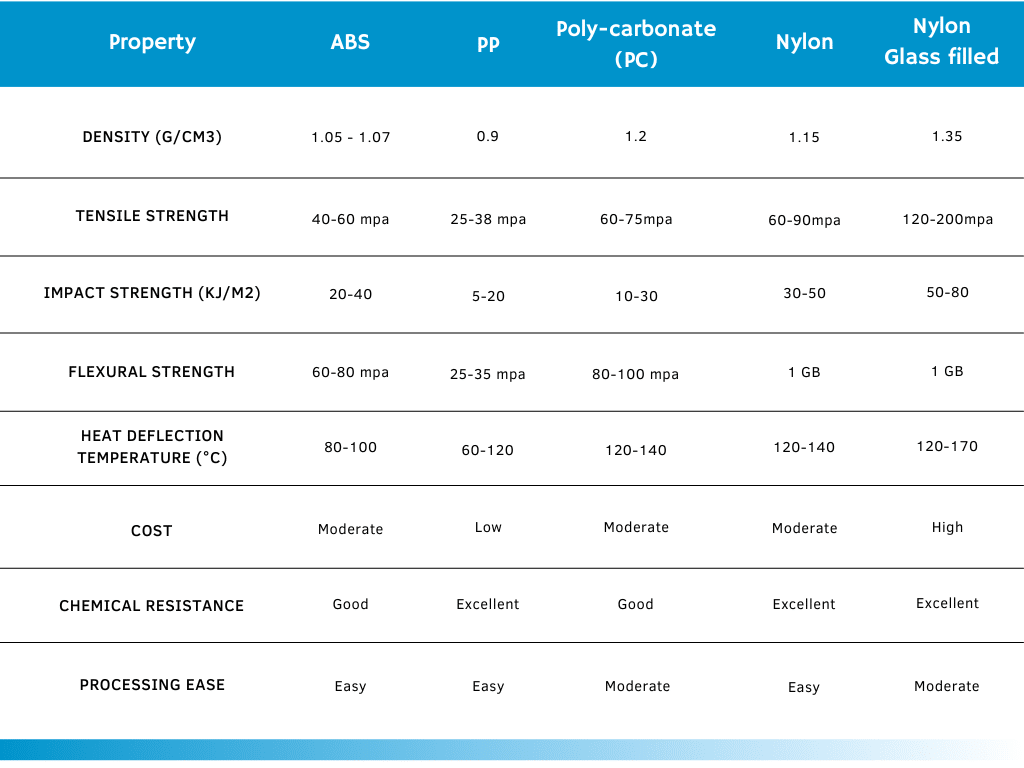