With the rapid-spreading adoption of 3d printing technology across all industries, 3d printers have been hyped as a future everyday use machine as the ink jet printer you put on your home table or office desk today. Yes indeed, why should you bother calling the ever-occupied customer services and waiting for two weeks to get a spare knob for your broken dishwasher when you can print it right at home within a couple of hours? The 3d printed products have proved to be of great advantage in various fields. This idea of convenient and free 3d printing at home sounds very attractive, but is it truly feasible?
How does traditional manufacturing works?
The current mainstream technology in the manufacturing process is plastic injection moulding. It takes four main steps to launch a new product:
- Specification
- Design
- Engineering
- Production
The specification refers to the set of activities to define the high-level and detailed-level of product functions:
- Dimensions,
- Mechanical strength,
- Visibility
In other words, what the products should do to meet the perceived market needs. Based on the specifications, a team of design engineers will go through every detail of the specifications and turn them into a particular product that meets the requirements at the same time can be manufactured in the volume under current machining conditions, considering factors like materials, mechanical properties, software applications, costs, time to produce, etc. Then a group of product engineers will take care of the multi-step engineering process including manufacturing samples, several rounds of the quality check based on the feedback loop, and final products. They also need to deal with issues of cost, producibility, performance, reliability, serviceability, expected lifespan and user features.
After all these steps, the production will begin. But till then there are still possibilities of problems that occur due to neglects of one or two tiny details in the former steps and the manufacturing process will loop back to the beginning of the process.
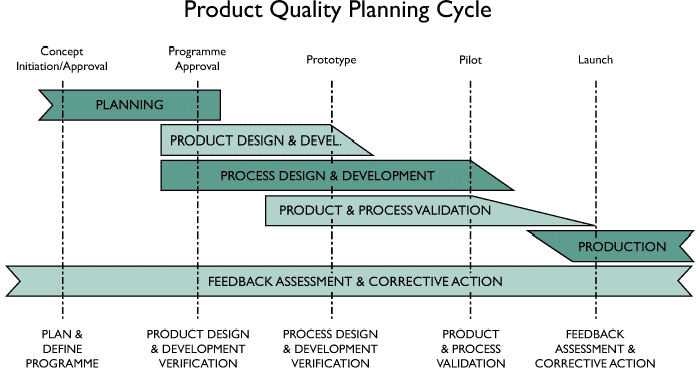
Product Quality Planning Cycle
Difference of 3d printing from the traditional process
To much concern, there is no major difference. 3d printing shares the main features of any other traditional manufacturing process. 3d printing demands the same level of expertise that involves groups of multi-disciplined engineers. It is therefore unreasonable to imagine that industrial-level production by 3d printing will be performed anytime soon in customers’ houses! Ensuring the consistent quality of final 3d printed products requires both steps 4 and 5 of the APQP process: ensuring product & process validation, then monitoring production performances and applying corrective actions in case of process divergence.
How do we make it possible to make 3d printed products on-demand and directly in where the demand is?
To do so, the quality assurance system shall at least cover two aspects:
- Ensuring that the outcome of industrialization (the process of converting a design into a production process) fulfills the design specifications.
- Monitoring quality consistency of the 3d printed products in the distributed production process.
During industrialization, engineers outline the optimum set of parameters that will define how the part will be printed by the 3d printer. These include variables such as printing temperature, speed, and tool path. Factors that are taken into account while defining these parameters include part geometry, mating features such as keyways, and the required mechanical strength. This process can be re-iterative to ensure the final print is of the highest quality. Finally, a set of final parts are produced, and their dimensional and mechanical features tested and verified,
before the set of computer instructions or ‘G-code’used to print the part is finalized.
When the part is required to be produced at one of the 3d printing service providers, the final G-code is transferred securely through an online 3d printing cloud service. Before production commences, the printer(s) at the provider is calibrated to ensure that their X, Y, Z calibration, and extrusion state are within acceptable bounds. This is carried out by running a set of calibration tests on the printer(s). The same set of calibration tests are conducted on a daily, weekly and monthly basis. It is done to ensure that the industrialization process is carried out on well-tuned and properly functioning printers.